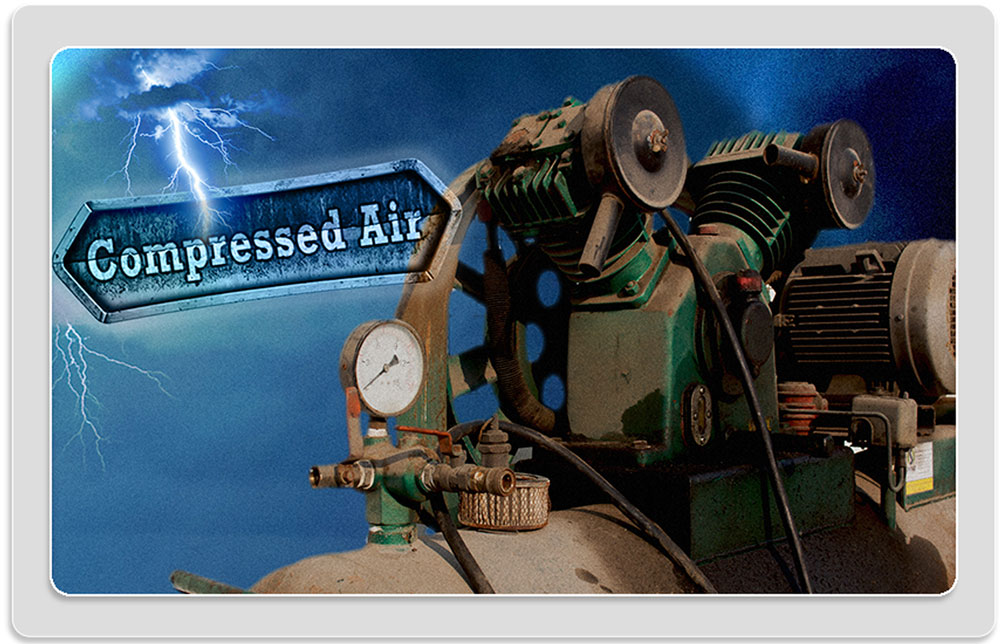
Manufacturers take great pains to select the most effective adhesives to use with their fluid dispense systems in order to ensure the quality of their bonds and, ultimately, their products. As much effort as they put into evaluating adhesives, there are still far too many instances in which fluid formulations fail. Very often the cause of these failures eludes manufacturers even when it’s staring them in the face—it’s the syringe and the air driven fluid dispense systems they entrust to deliver quality bonds.
The telltale signs of these costly breakdowns
Before fluid formulations flat out fail, manufacturers begin to experience issues with reliability and quality control. They come in the form of variations in viscosity and dot size, dripping and waste of the material, and changes in homogeneity. It doesn’t take long for all this to take its toll on the accuracy and repeatability of fluid dispense systems. These troubles are the result of the intensity of compressed air being pumped into the syringe, which over time dramatically impacts fluid formulations.
Syringes and fluid formulations are under attack
The surge of air pressure into a syringe is violent. It crashes the piston into the fluid creating tremendous internal fluid pressure. It does so repeatedly, down and back, over and over again, which creates a phenomenon known as “piston bounce”. One way to envision this is to think about how butter is made in a churn where the wooden piston is rammed into the cream at a rapid rate to heat the liquid until it thickens and eventually becomes butter.
This is okay when making butter, but it has ruinous results when working with assembly fluids. As with butter, the piston bounce causes the fluid to heat, which in turn, causes the chemistry and the bonding properties of the formulation to change along with it. This puts the warranties protecting assembly fluids at serious risk, which can create similar concerns to the warranties safeguarding the products manufacturers sell to their customers.
It takes a gentle approach to protect fluid formulations
Fishman® Corporation developed a system that replaces compressed air. It’s the SmartDispenser® with AlgorithmicControl™ and patented AirFree® Technology. This one-of-a-kind solution is comprised of a Linear Drive System (LDS) utilizing a motor, lead screw and algorithms. A forward motion algorithm installs a gentle ramping motion, which helps eliminate stress to the fluid.
The reverse motion of the piston is controlled by an attached lead screw, which prevents the piston from wildly recoiling, while a reverse motion algorithm controls the speed. The gentle ramping motion of the LDS is the most effective way to protect the formulation and bonding properties of assembly fluids manufacturers count on each and every day.
Additional information on this important topic is a click away
To learn more about how best to protect fluid formulations and the products you manufacture, download the recently published White Paper: Manufacturers are unwittingly putting fluid formulations at risk of failure. Reading it will enlighten you to how the SmartDispenser® and its LDS offer a level of protection that can’t be matched by any other fluid dispense system on the market today. You can also find additional information on this and other topics at fishmancorp.com.