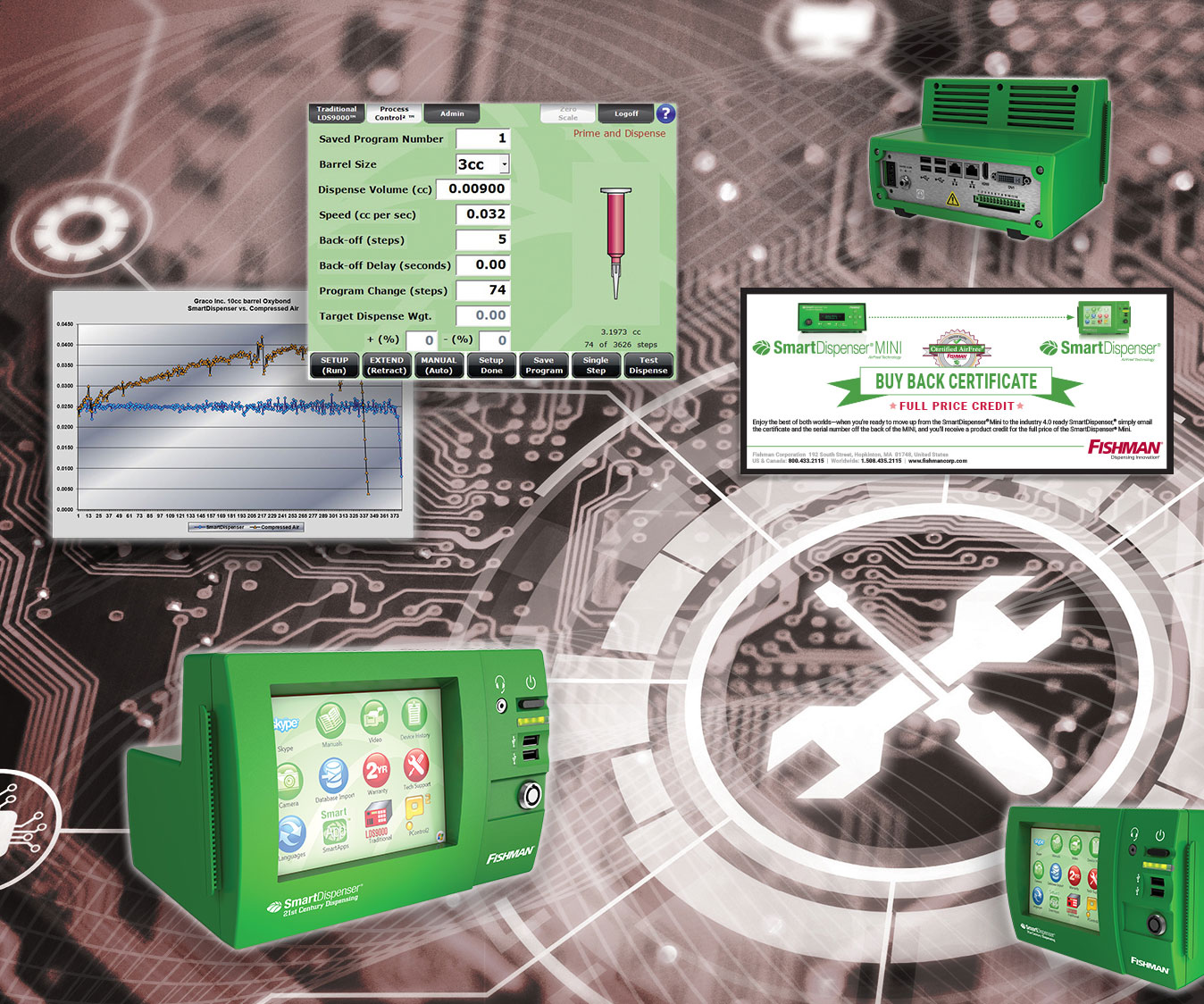
Fishman® Corporation has long been known for its innovative fluid dispense systems. But there’s another part of our organization that gets high marks once it’s brought to the attention of our customers: Fishman®’s Tech Service Department. It’s held in such high regard because of the many outstanding sales and support solutions it offers customers before, during, and long after they purchase their SmartDispenser®s.
Performance is validated even before the SmartDispenser® is purchased
Potential customers are amazed when they learn about the Validation Support Program (VSP). That’s because it offers them a no-risk, no-cost way to purchase the SmartDispenser®. With VSP, validation testing is conducted by Fishman® Application Engineers at our facility. Our engineers use the potential customer’s specifications, fluid, and sample parts to program the SmartDispenser® they’re thinking of purchasing.
Once testing is completed, the results and sample parts are turned over to the customer’s engineering staff for quality inspection. As soon as the parts are approved, the SmartDispenser® is delivered and installed at their facility and, within minutes, it’s up and running. The reason the installation goes so smoothly is the fact that the original test reports provide baseline statistical data that can be matched against the customer’s validation testing. This will prove the SmartDispenser® performs exactly the same at their facility as it did in ours.
With VSP, validation is virtually certain because of the AlgorithmicControl™ feature of every SmartDispenser®, which allows algorithms to be applied to a mechanical drive, thus enabling it to achieve optimum precision in fluid dispensing. That’s a feat no fluid dispense system reliant on compressed air can hope to match.
After-the-sale tech service and support that customers cheer
It all starts with, what else, installation support— Once the purchase of the SmartDispenser® is made, our Tech Service Department stands ready to offer customers any help they may need with installation which, frankly, will be rather quick and easy thanks to VSP and AlgorithmicControl™. Of course, should any issues come up, customers are put at ease thanks to the swift, but thorough work of our skilled fluid dispense team.
Proper programming is key for fluid dispense systems to shine— That goes for wherever SmartDispenser®s are at work in the world. When changes need to be made, all a customer needs to do is send the Fishman® Technician the program they’re running, along with their fluid, dispense tip types, and syringe size. With that information, the technician will set up a duplicate SmartDispenser® in the Fishman® laboratory, where they’ll recreate and resolve the issue, then send the new dispense program with any needed adjustments back to the customer, thus ensuring that exact duplication is possible worldwide.
When things happen, we always happen to be there to help— Customers can always count on our Tech Service Department to be available to make program adjustments or run diagnostics to make certain everything is operating properly. Some customers let us do this by keeping their SmartDispenser® online at the end of their production day. They like this approach because the SmartDispenser® runs on the Windows® 10, which employs the same protocols that the IT departments of most companies use to connect any computer to their own local secure server. This allows our technician to log on and make any necessary modifications overnight. That way, when customers return to work the following morning, their SmartDispenser®s are good-to-go.
Assistance can be provided during business hours as well— All customers need to do to “show” the technician the issue they’re having is to put their SmartDispenser® online using LogMeIn’s Rescue program. This permits instant messaging to occur between our technician and our customers. It also gives the technician the ability to have remote control of their SmartDispenser®, along with access to all reports and logs on it, ensuring any issues are taken care of quickly.
Down-the-road programs that customers give big thumbs up to
Further along as the production needs of customers evolve, they know they can rely on Fishman® to make the transformation both easy and affordable. Two ways how this is accomplished is with the Fishman® Buy Back and Upgrade Programs.
The Buy Back Program enables customers to upgrade their original purchase to the next level of production performance. Customers that purchase the SmartDispenser® MINI™ can upgrade to the SmartDispenser® Benchtop System by simply taking advantage of the Buy Back Program.
Customers that have the SmartDispenser® Benchtop System, and who at a later point want to automate their assembly process, can easily do so by upgrading to and integrating their current system with the SmartAutomation™ Platform.
Both are easy, affordable and offer further proof that the SmartDispenser® is the most flexible fluid dispensing system available today.
For more about Fishman®’s Tech Service Department, feel free to contact Dave Thomas, Tech Support, dthomas@fishmancorp.com, 508-686-5065 or Meghan Malkin, Tech Support, mmalkin@fishmancorp.com, 508-686-5066. They look forward to being of service to you.